The future of energy storage in the U.S. hinges on a small but essential component: the battery electrolyte. The electrolyte touches every part of a battery cell and provides the critical function of transporting lithium ions between the anode and cathode electrodes, allowing batteries to charge and power devices during discharge.
As America races to lead in battery innovation—advancing new technologies from long-range drones to AI data centers to new secondary power sources supporting the grid, the need for high-performance, domestically sourced electrolytes has become urgent.
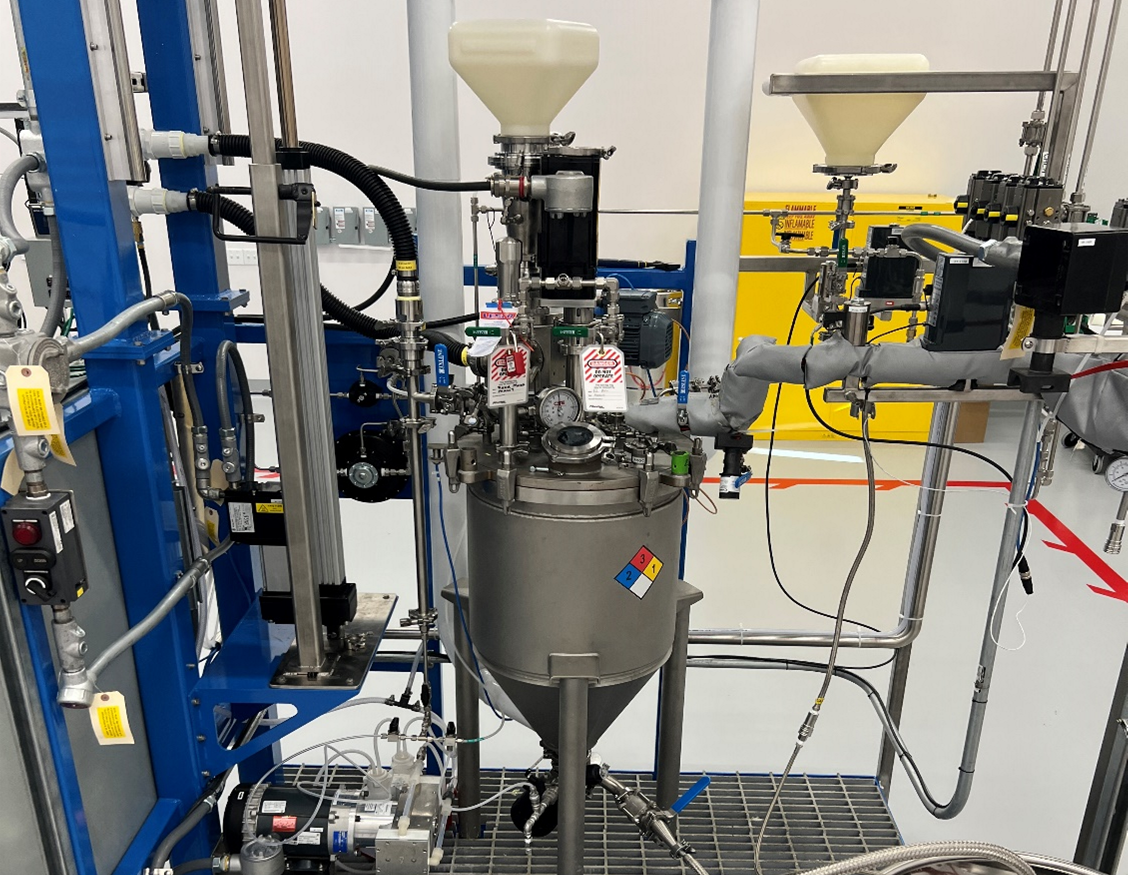
Orbia’s custom electrolyte offering is powering the next generation of batteries.
Emerging technologies rely on advanced battery materials including fast-charge anodes, high-capacity silicon anodes and high-voltage cathodes that require specialized electrolytes to unlock their full potential. These batteries must not only last longer and charge faster, but also operate safely under extreme conditions, including high temperatures, rapid charging/discharging and sustained power output. While many U.S. companies work to develop these next-generation batteries, they’ve faced a critical obstacle: limited domestic access to the customized electrolytes these innovations depend on.
Recognizing this market need, Orbia’s Fluor & Energy Materials business has developed a new custom electrolyte offering—designed specifically to support the evolving needs of next-generation battery developers in the U.S. For the first time, companies can source small- and medium-batch electrolytes domestically, tailored to their exact specifications. This new capability not only accelerates innovation but also strengthens the nation’s battery supply chain at a critical moment.
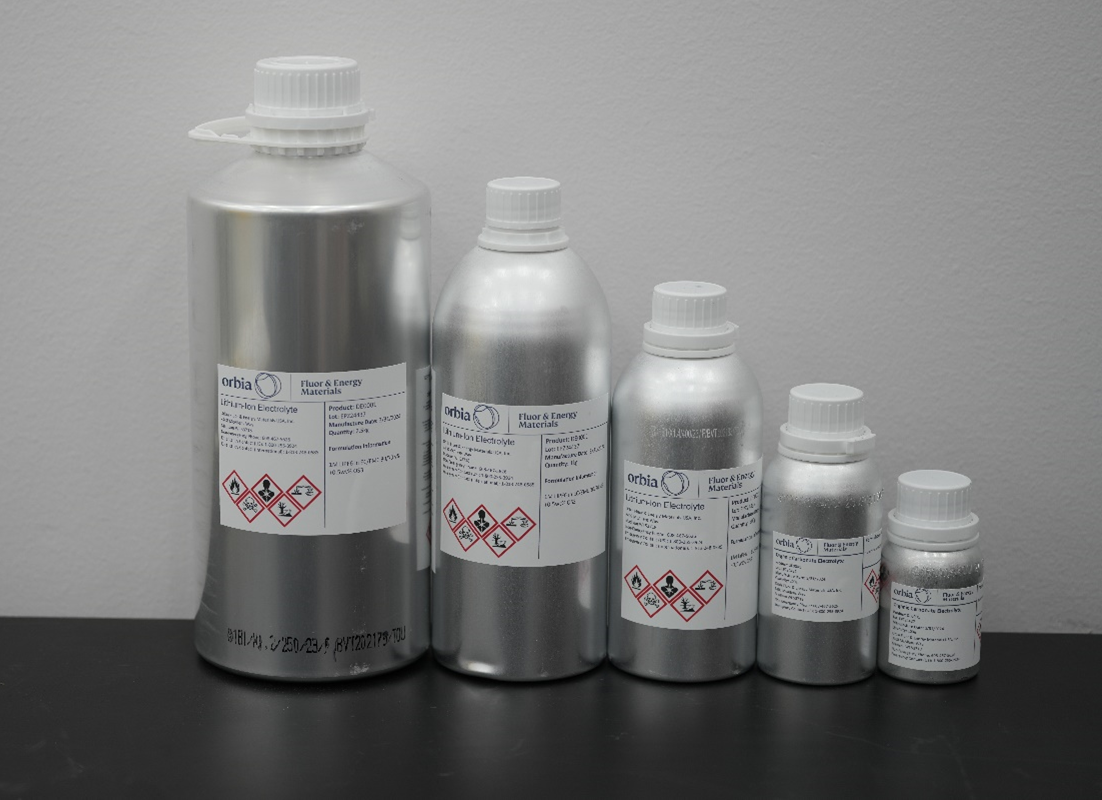
Orbia’s custom electrolyte business offers customers a wide range of packaging options, from 100g – 2.5kg bottles, as well as 20kg – 200kg kegs and drums to support early-stage R&D requirements, pilot facility needs and full-scale mass production.
Removing Industry Bottlenecks with Rapid-Response Electrolyte Production
Prior to 2023, U.S.-based battery research facilities, prototype centers and manufacturers serving niche applications faced significant challenges sourcing electrolyte. With major Asian producers increasingly focused on high-volume electric vehicle markets, domestic innovators were left reliant on imports—often facing 8–12 week lead times, uncertain delivery schedules, intellectual property loss and the risk of product degradation during shipping.
Orbia has changed that. As one of only a few companies offering custom electrolytes within the U.S., Orbia supports fast innovation cycles through a rapid-response business model. Orbia delivers in less than four weeks, enabling quick-turnaround supply of small and large quantities of electrolytes to support R&D, prototyping and full-scale production. Speed not only preserves product quality and shelf life but also empowers the U.S. battery ecosystem to push technological boundaries well beyond today’s capabilities.
The offering has received strong customer support, with an ever-growing customer list including Navitas Systems, Enovix, Lithion Battery and Forge Nano. Since opening in 2023, the facility tripled output in 2024 and is on pace to double output again in 2025. Today, the facility provides electrolytes to more than 100 customers in the U.S.
Behind this rapid customer adoption is a strategic differentiator: Orbia’s integrated supply chain and secure access to essential materials like fluorine.
Orbia ships custom electrolyte formulations in four weeks or less after an order is placed.
Making a National Impact with a Secure Supply Chain
Orbia’s upstream integration in critical raw materials—particularly fluorine, a vital element used in electrolyte salts and other battery components provides a key advantage. Orbia’s North American fluorine supply chain is anchored by its fluorspar mine, which is the world’s largest and allows us to supply 18% of the world’s fluorspar each year.
One of the most important and costly electrolyte ingredients is lithium hexafluorophosphate (LiPF₆), the industry-standard salt used in most lithium-ion batteries. Today, global production of LiPF₆ is concentrated almost entirely in Asia, with China alone accounting for over 90% of supply—posing a significant risk to U.S. battery makers looking to scale.
To help close this gap and localize a critical link in the battery value chain, Orbia is advancing plans to build a LiPF₆ production facility at its St. Gabriel, Louisiana site. This investment helps ensure a more reliable supply for U.S.-based battery manufacturers, particularly as many plan to expand or manufacture new U.S. battery plants within the next decade.
Scaling Innovation: A Homegrown Success Story
Orbia’s investment in custom electrolytes builds on a foundation of innovation that began well before Orbia’s current market expansion. The custom electrolyte business originated from Silatronix, a Madison, Wisconsin–based startup that Orbia acquired in 2021. Silatronix pioneered a unique electrolyte technology for high-performance battery cells and proficiency in electrolyte formulation and characterization.
Recognizing the market opportunity, Orbia combined its global capabilities and expertise with the technical foundation developed at Silatronix to beta-launch the custom electrolyte offering in 2023. Following this successful launch, Orbia constructed a new 11,000 square foot Madison Production Center to house custom electrolyte production. The new business received an $8.4 million U.S. Department of Defense grant supported by U.S. Senator Tammy Baldwin of Wisconsin which highlights its critical role advancing and securing the battery material supply chain. The grant expedited construction, which Orbia expects to complete at the end of 2025 with a production capacity of approximately 400 tons per year.
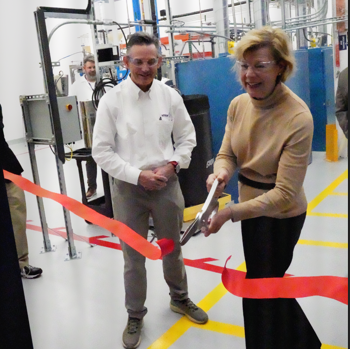
Senator Tammy Baldwin cuts a ribbon officially opening a newly built section of the custom electrolyte production facility.
Behind the Blend: What It Takes to Make High-Performance Electrolytes
Despite its apparent simplicity, producing custom electrolytes is technically complex. Electrolytes have three components: the salt (for example LiPF6), solvents (ethylene carbonate or dimethyl carbonate) and additives (like vinylidene carbonate). Each component plays a distinct role in battery performance: the salt supplies lithium ions, the solvent moves them through the battery and the additives fine-tune how efficiently they flow during charging and discharging. The specific anode and cathode electrode materials and application requirements determine the selection of each of these components.
Orbia stocks all the most commonly used salts, solvents and additives and blends them in the ratios requested by customers. Some formulations may use Orbia’s proprietary solvents and additives developed to meet demanding performance goals. These include Orbia’s OS3® electrolyte additive, which is designed to enable high-capacity silicon anodes to cycle without gas generation in very high energy density cells and Orbia's Koflyte line of fluorinated solvents which is designed to operate at higher voltage and enable faster charging.
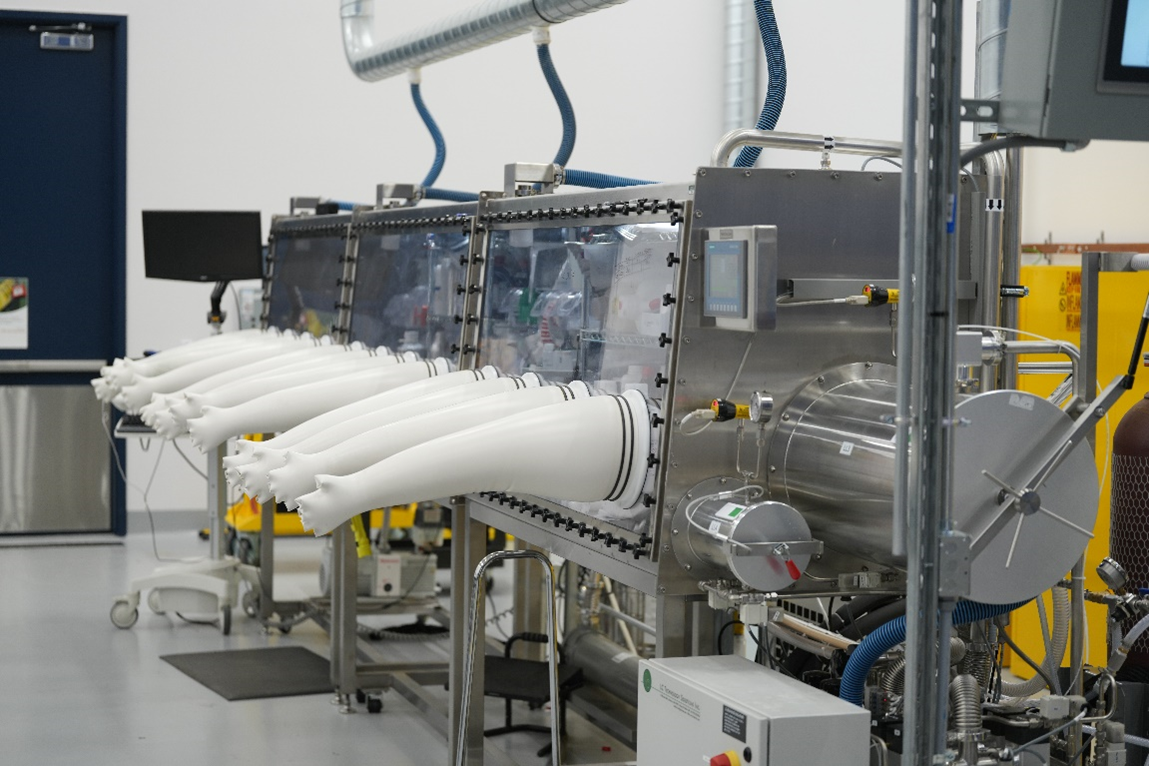
Orbia produces electrolyte formulations in a controlled environment inside glove boxes at the custom electrolyte production facility.
“Making a high-quality custom electrolyte is a multi-step process. First, we have to procure the highest-quality electrolyte components and confirm their purity. Then, technicians blend the components together with care and precision to ensure formulation accuracy while preventing unwanted degradation reactions. Finally, Orbia scientists conduct a series of analytical characterizations on the blended electrolyte to confirm electrolyte quality. Our Madison facilities are designed to efficiently carry out all of these steps while ensuring the highest levels of safety and process control supported by state-of-the-art equipment and technical expertise.”
—Carl Thoemmes, Orbia Fluor & Energy Materials Battery Material Business Development Director
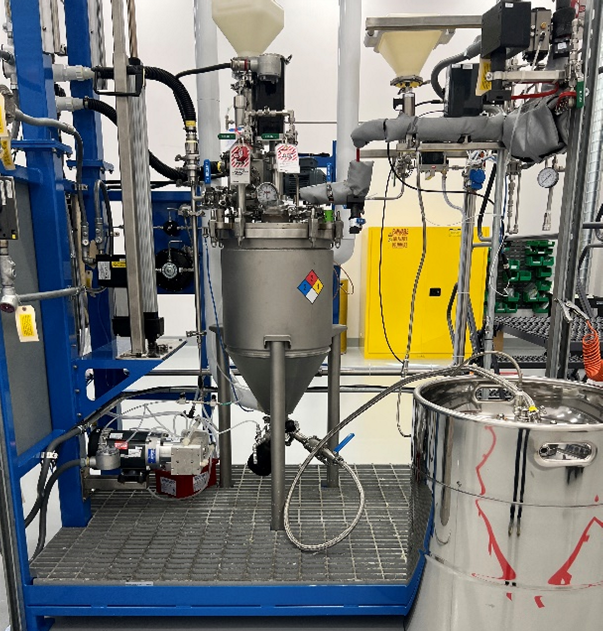
Orbia is leading the industry in developing custom electrolyte production improvements. For example, Orbia has designed a semi-automatic mixing rig that can efficiently and safely mix salts, solvents and additives with high precision.
Smart Chemistry, Better Batteries: R&D at the Madison Technology Center
In addition to supplying customers with their preferred electrolyte formulations, Orbia's scientists and engineers leverage their decades-long expertise to optimize electrolyte formulations for specific applications.
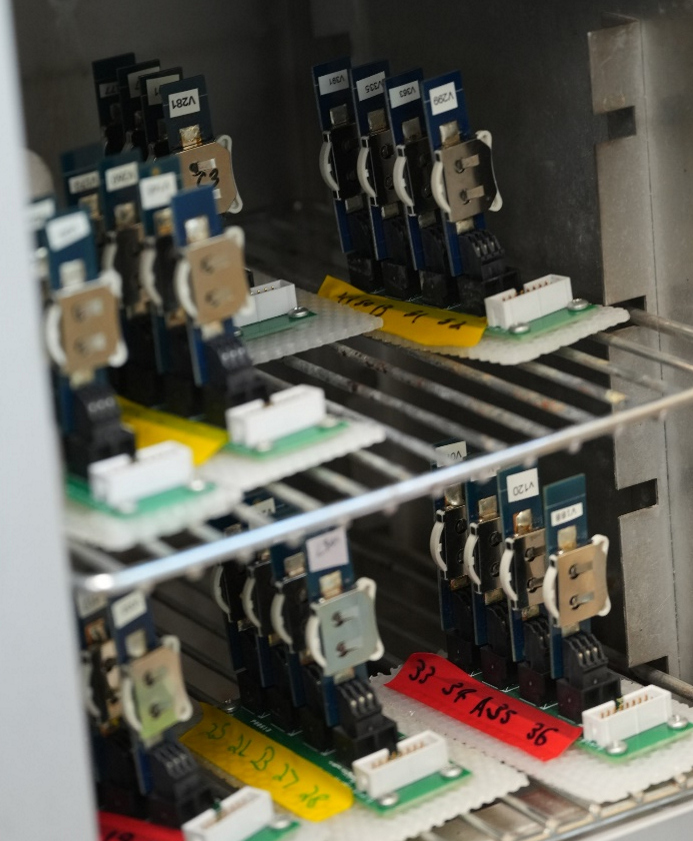
Initial screening of electrolyte performance in small coin cells.
At Orbia’s Madison Technology Center which focuses on R&D, Orbia scientists follow a successful methodology for optimizing electrolytes. Orbia starts with in-depth collaboration with customers to identify all aspects of their battery cells from active materials and current performance challenges to target improvements and the specific operating conditions the cells must endure. Based on these insights, Orbia’s scientists develop a list of electrolyte formulations to test for optimal performance by selecting suitable salts, solvents and additives in varying ratios.
The next step in the process is evaluation of the different electrolyte formulations under relevant conditions. Scientists blend sample batches of electrolyte formulations in Orbia’s lab and test them in representative battery cells under application-specific conditions of duty cycles, voltage ranges and temperatures.
After testing, post-mortem analyses with advanced analytical techniques reveal how the electrolyte interacted with the active materials and influenced cell performance. This comprehensive approach allows Orbia scientists to rapidly iterate on the electrolyte formulation to arrive at the optimized solution.
After developing a successful formulation, Orbia will produce it at the Madison Production Center, a short 15-minute drive away.
Orbia has several battery testers onsite that can determine how a battery will perform over time in a variety of conditions.
As the energy storage landscape continues to evolve, Orbia is investing in solutions that will shape batteries far into the future. The company is pursuing targeted electrolyte development programs focused on enabling low-cost, manganese-based cathodes, high energy density anodes such as silicon and lithium metal and military-grade batteries capable of operating across a wide temperature range.
With growing customer adoption, federal support, a secure supply chain and state-of-the-art production and innovation facilities, Orbia is building a foundation for long-term leadership in the U.S. energy materials landscape, one custom electrolyte solution at a time.
This article is part of Orbia’s Megatrendsetters blog series, which explores how Orbia’s solutions are driving the transformative forces, or “megatrends” that are advancing our society, from decarbonization and the circular economy to shifting supply chains and agribusiness to global water and digitalization. To learn more about Orbia’s custom electrolyte offering, visit the Orbia Fluor & Energy Materials’ website here.